W. Sarrus, a French bandmaster, invented the Sarrusophone and had it constructed for
him by P.L. Gautrot, Sr. It was patented in 1856 and is a unique
instrument in that it is a brass instrument with conical bore and
a double reed embouchure. There are eight voices of the
instrument from sopranino to subcontrabass. The fingerings and
the B-flat registers are all comparable to the saxophone. The
smaller instruments look very much like the soprano saxophones.
The above definition was taken from the Terminology Collection of Online Dictionaries
at http://www.uwasa.fi/comm/termino/collect.
The Sarrusophone is no longer made, but we at Oberloh Woodwind and Brass Works have become extremely
proficient at restoring these fine instruments. We have recently
been asked to restore a 1922 Conn ContraBass Sarrusophone, and
will be bringing pictures of that work in progress for your
enjoyment.
Click on the thumbnails below to see the full size picture.
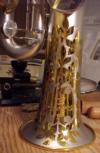 |
To the left are a number of thumbnail images. The first three
we chose simply because, in our opinion, they are the most beautiful.
The finish of the instrument is not original. We chose it to be
satin silver with burnished highlights and 24 karat gold overlay.
We chose this finish not only because it was so beautiful, but also
to cover a host of sins perfomed by countless repairs enacted over
the past 115 years. |
|
|
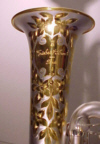 |
This instrument was manufactured by Triebert & Cie. of France. Made in the early
1880's, about the time that Gautrot purchased the firm. This image
demonstrates the artistry of the master engravers of the age. |
|
|
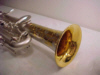 |
Staying with the common theme of our desired finish, it is only appropriate to gold finish
the inside of the bell. The original finish of this instrument was
most likely raw brass. |
|
|
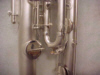 |
The most challenging process
to be performed during this restoration, hands down, was the
fabricating of the water key u-tube. Completely BY HAND!
Raised from flat brass sheet stock, the conical tube was formed and
bent 180 degrees. The process took 10 VERY intense hours to complete.
|
|
|
 |
The next several images are shown to emphasize the details addressed throughout the
rebuilding of this instrument. The work involved called for the
removal of ALL soldered components, i.e., posts, toneholes,
guard mouldings and ferules. |
|
|
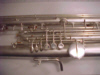 |
With the removal of all soldered parts, we were able to concentrate on the smallest of
defects in the body tubes. This allowed us to present a final finish
to the instrument never imagined. |
|
|
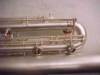 |
After all the tubes, bows and bell were complete, the arduous task of remounting all toneholes,
posts, and other assorted bits and pieces could take place. In our
shop, this process requires an emphasis on parallels and right angles.
This ensures the instrument be dimensionally correct when
completed. |
|
|
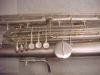 |
After 115 years, you might think the keys would be pretty badly worn...and you'd be right! All
key work was completely refitted and in many cases new metal was added
at the worn ends to ensure a smooth, long lasting, precision fit. |
|
|
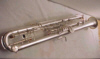 |
Once the body had been reassembled (completely resodlered), very careful polishing was
performed, with special emphasis on not overbuffing. Our attitude
is that the instrument has made it 115 years, we want it to last at
least another 115, so leave the metal on the horn! |
|
|
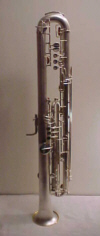 |
The restoration of this bass sarrusophone employed a number of very talented artisans.
Stephen McComas, Daniel Oberloh, Tom Green and the staff at Anderson
Silver Plating Co, Inc. of Elkhart, Indiana. The restoration took
place over a period of 18 months.
A note to the viewer: there has been a great deal of talk about refinishing brass instruments.
Many have said: "to refinish is to ruin". Our attitude is: "Why would
you want to do a restoration half way?" When this instrument arrived
at our shop, it did work...barely. The owner, Michel Jolivet,
wished the instrument be raised to a new glory, not only in its
playability, but also in its aesthetic appeal. The process of
refinishing instruments requires a mastery of metalworking
ability, as well as a great deal of self-control. When done properly,
an instrument should always play as well or better when leaving the
shop then when it was new, given a good basic design. We
would like to thank Dr. Jolivet for his patience, and trust in
allowing us the opportunity to perform such a worthwhile task. |
|
|
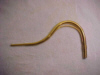 |
A side note: When it comes to double reeds, all of the beautiful pad work and plating won't do
anything for the intonation if the bocal is not right. The original
put the horn 20-40 cents flat, and caused it to lack in center. So,
we made a new one. |
|
|
 |
The new bocal is fashioned after the original. It was produced primarily through the same
technique, although we changed the length and taper ratio.
Raised from flat brass sheet stock, the seam was silver braised and
hand worked on a specially made steel mandrel. Telescopic tubing was
fabricated for the receiver, and it was embossed with the company family name, after all, we
designed and made it! Finally, it was finished in 24 karat gold.
|
I hope you enjoyed this page as much as we enjoyed the restoration process and the opportunity to show
off the ability of our craftsmanship! If you have any questions regarding this
job or any others, please feel free to email us anytime. Thanks.